Why Ceramic Injection Molding?
The CIM (Ceramic Injection Molding) process has the following advantages over other manufacturing processes in economic and technical terms
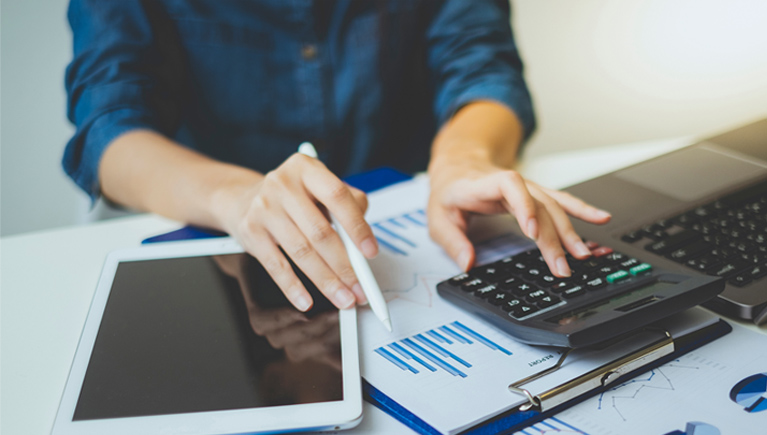
Costs
Efficient process for series production:
- One-time investment in mold
- Multiple cavities
- Fast production cycles
- Optimal use of raw materials
- Minimal post processing
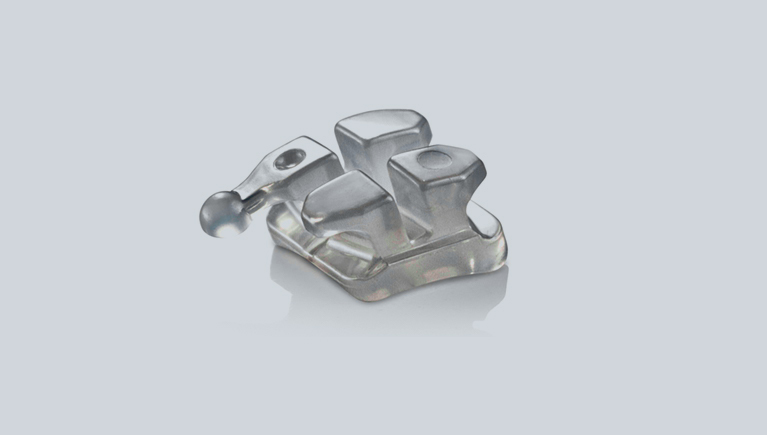
Near Net Shape
Thanks to the CIM process, we can produce complex small parts in large quantities.
Molding to near net shape allows a significant reduction in post-processing steps. High surface quality is also achieved with no additional reworking.
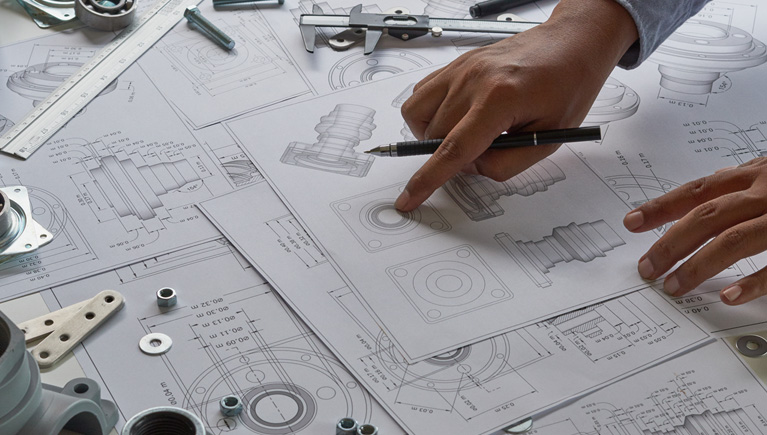
Small Tolerances
Smallest tolerances reliably reproducible from lot to lot:
- CPK studies to desired dimensions
- Surface roughness < 0.0175 Ra
- Smallest bores ±1µ
The Benefits of Using Ceramic Injection Molded Ceramics
Ceramic Injection Molding is an advanced manufacturing process used for making parts in various shapes and sizes. It’s also known as ceramic transfer molding, which involves injecting molten material into a cavity formed by two halves of a mold. The mold is then closed and the injected material cools and hardens. Once cooled, the mold opens and the part is removed.
High Strength
Injection Molded Ceramics are made with a variety of materials, such as aluminum oxide (alumina), silicon carbide, zirconium dioxide (zirconia), and beryllium oxide. These materials provide strength and durability while being lightweight. They are also resistant to heat, chemicals, and corrosion.
Long Lasting Quality
Injection Molded Ceramics are used in a wide range of applications, including medical devices, aerospace equipment, automotive parts, and more. They are often preferred because of their longevity and durability.
Durability
Molded Ceramics are made with ceramic materials that are strong and durable. This means that they will last longer than other injection molded parts.
Low Cost
Ceramic Injection Molded Parts are also low cost compared to other injection molded parts. They are also easy to clean because they do not contain any toxic chemicals.
Easy To Clean
Our ceramics are made by Injecting Molten Ceramic into a mold cavity. This process creates a product with a smooth surface finish and no seams. These products are used in a wide variety of applications such as medical devices, automotive parts, and consumer goods.